
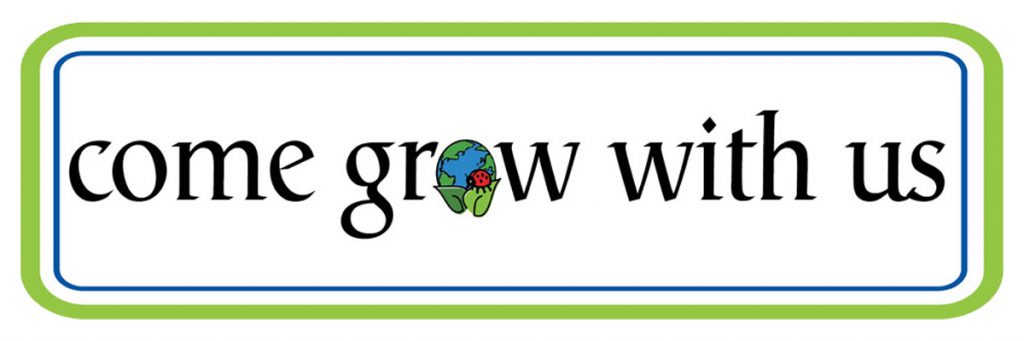
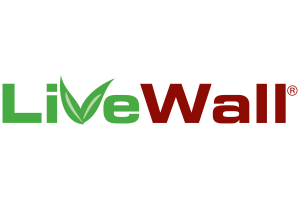
Careers
Thank you for your interest in employment with Hortech, LiveRoof, and LiveWall.
We’re passionate about people, plants, and our planet. We aim to create a greener, healthier, and more sustainable world. If you share in our passion, then consider joining our team of like-minded, hard-working individuals as we supply an array of products and services designed to make the world a better place.
Hortech is a wholesale production/propagation nursery started in 1983. We grow a broad and interesting line of ground covers, ornamental grasses, climbing vines, and ferns. LiveRoof specializes in a fully vegetated modular green roof system. LiveWall specializes in a proven vertical green wall system that works very well. We pride ourselves on providing clients with premium, earth-friendly, quality products with steadfast service with an emphasis on superior customer service. We offer both seasonal and non-seasonal positions of varying responsibilities and strive to hire diligent, highly motivated individuals.
We’re located 30 minutes West of Grand Rapids and 15 minutes South of Muskegon.
If you have any questions, please contact us at (616) 842-1392.
Here are some reasons why you might want to work here:
Continual Growth | Culture | Competitive Compensation |
---|---|---|
|
|
Benefits depend on position and employment status |
Continual Growth |
|
Culture |
|
Competitive Compensation |
Benefits depend on position and employment status |
Check out our open positions, below! For general applications for consideration of a non-open position, please click here. We will hold onto your application for 6-months.
We also have other career opportunities that you might be interested in now or in the future. Career opportunities exist in the following areas:
Multiple summertime positions are perfect fits for students or other people seeking a seasonal summer position.
Please note: Our application process began when you expressed your interest in receiving an application. Now, should you still have an interest in becoming a member of our staff, please scroll down and fill out the application below and read carefully before submitting. Or dial (800) 875-1392 for other options.
We are an equal opportunity employer.
Application
We are always looking for motivated people to come grow with us. If you are highly interested in joining our team and making a positive impact in our world, please complete the form below.
Once you submit your application three steps will take place:
- You should receive an email that confirms receipt of your application
- A real person reviews your application (we don’t use robots)
- Depending on your qualifications we decide what career path might fit you the best.
We may not always have an available position you’re seeking at the time you apply, but we file your application under positions that seem like a good match or that are listed on your resume/application. This way when a position does become available, we search our database for people that match our search. However, we don’t use search engines or optimized keyword search software. We believe that it’s best to review each candidate’s qualifications by reading your application/resume. The people that tend to get interviews are the ones that follow-up. The people we want as part of our team are serious about our mission and focus: We aspire to be usefully innovative leaders in the industries that we serve. We love plants, enjoy the outdoors, maintain positivity, and give an honest day’s work.
Please download an editable PDF of our application below and use the form to submit your application (required) and resume (optional but may be required after, depending on position). Our human resources department will contact you shortly after submission.
Hint: we prefer that you complete all applicable fields on the application. If not applicable, we prefer “N/A” versus leaving a blank space. For example, if you do not have a telephone number, please enter N/A and provide a way for us to contact you in the notes section at the bottom of the application.